High-Pressure Mini Hydraulic Cylinders Revolutionizing Coal Auger Drills
Coal mining’s relentless push for efficiency faces a critical barrier: space. Underground environments demand equipment that’s powerful yet compact, robust yet lightweight. At the heart of coal spiral drills (augers), hydraulic cylinders face this challenge head-on. The industry’s answer? High-pressure miniaturization – delivering equal (or greater) force from smaller, lighter packages. Here’s why it’s a game-changer and how it’s achieved.
The Driving Forces: Why Smaller & Stronger?
Space Constraints: Tunnel dimensions limit equipment size. Compact cylinders enable agile, maneuverable drills.
Weight Reduction: Lighter cylinders simplify transport, installation, and handling in confined shafts.
Enhanced Flexibility: Smaller actuators allow for more complex drill head designs and positioning.
Higher System Pressure: The key enabler – systems pushing 35 MPa+ unlock massive force from reduced cylinder footprints.
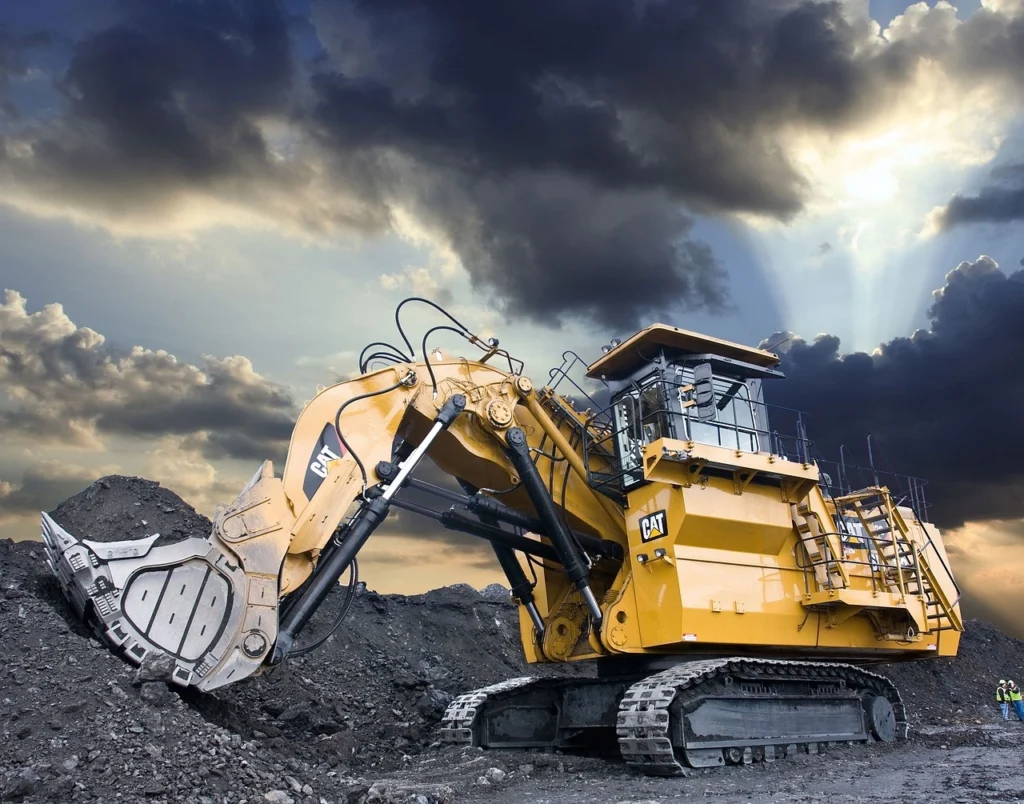
Engineering Breakthroughs Making it Possible:
1. Advanced High-Strength Materials
The Challenge: Thinner walls needed for size/weight reduction CANNOT compromise strength under extreme pressure.
The Solution:
Special Alloy Steels: Ultra-high-tensile alloys for cylinder barrels and piston rods.
Precision Metallurgy: Optimized grain structures and heat treatments enhance durability.
Result: Significant wall thickness reduction while maintaining or exceeding burst pressure ratings.
2. Precision Manufacturing & Next-Gen Sealing
The Challenge: Extreme pressure (35MPa+) demands flawless internal surfaces and seals that won’t extrude, leak, or wear prematurely.
The Solution:
Nanometer-Smooth Honing: Achieving near-perfect bore roundness, straightness, and surface finish (Ra < 0.1 µm) to prevent seal damage.
Advanced Seal Tech:
High-Pressure Polyurethanes: Exceptional resilience and extrusion resistance.
Reinforced PTFE Composites: Low friction, high wear resistance, minimal stick-slip.
Asymmetric Seal Designs: Pressure-optimized profiles that actively reinforce under load.
Result: Zero-leak performance under sustained ultra-high pressure, maximizing efficiency and lifespan.
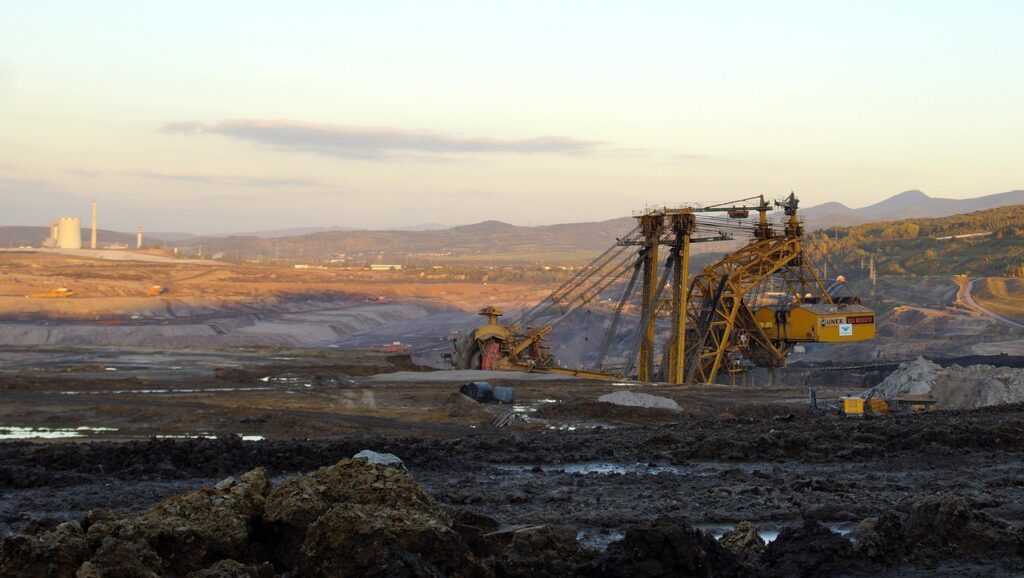
3. Compact & Efficient Structural Design
The Challenge: Eliminating wasted space within the cylinder assembly.
The Solution:
Integrated Porting: Internal fluid channels replace bulky external manifolds.
Optimized Piston & Rod Design: Finite Element Analysis (FEA) shapes components for minimal material, maximal strength.
Space-Saving Mounts: Low-profile clevises, flanges, and trunnions.
Result: Dramatically reduced envelope size and “dead” volume, boosting power density.
The Impact on Coal Spiral Drill Performance:
Higher Power Density: Deliver more thrust/torque without enlarging the drill’s footprint.
Increased Maneuverability: Navigate tighter mine sections and complex seam geometries.
Reduced Downtime: Robust materials and sealing minimize failure rates in harsh, abrasive coal environments.
Lower Operating Costs: Weight savings cut fuel/energy consumption; reliability slashes maintenance.
The Future is Compact & Powerful
The push towards 35MPa+ systems and ever-more-miniaturized cylinders isn’t slowing down. Innovations in ceramic coatings, composite materials, and smart pressure management sensors are poised to take coal auger drill hydraulics to the next level.
Ready to Optimize Your Coal Drilling Hydraulics?
Embrace the high-pressure miniaturization revolution. Partner with experts who understand the critical balance of power, size, and reliability for underground success.