What Advantage Does A Hydraulic System Have Over A Pneumatic System ?
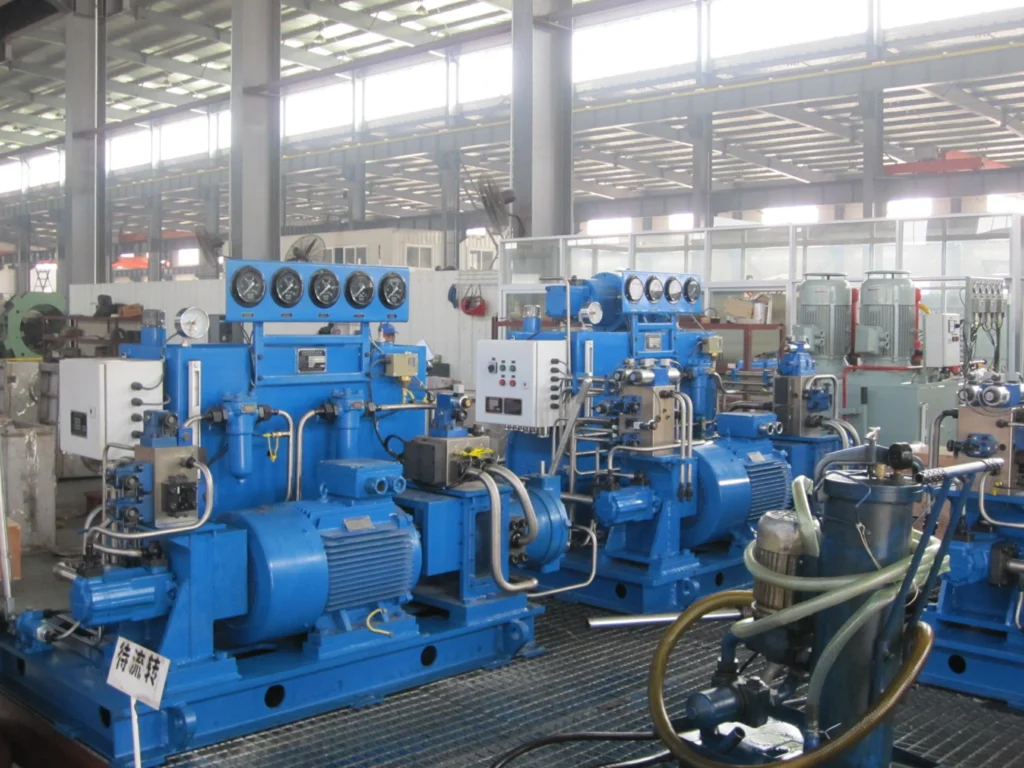
Hydraulic systems and pneumatic systems are both widely used in industrial and mechanical applications, but they have distinct characteristics that make each suitable for different scenarios. When comparing hydraulic systems to pneumatic systems, hydraulic systems offer several key advantages, particularly in applications requiring high force, precision, and durability.
The Primary Advantages Of Hydraulic Systems Over Pneumatic Systems
1. Higher Force and Power Density
Hydraulic Advantage: Hydraulic systems generate significantly greater force due to the incompressibility of hydraulic fluid (typically oil). They can operate at much higher pressures (3,000–10,000 PSI), enabling compact components to deliver immense power.
Pneumatic Limitation: Compressed air in pneumatic systems is compressible, limiting operating pressures to around 100–150 PSI. This makes pneumatics unsuitable for heavy-load applications.
Example: Hydraulic systems power excavators, cranes, and presses, while pneumatics are used for lighter tasks like clamping or packaging.
2. Precision and Control
Hydraulic Advantage: Hydraulic systems allow precise control over speed, position, and force. The fluid’s incompressibility ensures smooth, jerk-free motion, even under varying loads. Proportional valves and servo systems enable micro-level adjustments.
Pneumatic Limitation: Air compressibility in pneumatics leads to “springy” or less predictable motion, making precise control challenging.
3. Load-Holding Capability
Hydraulic Advantage: Hydraulic systems can hold loads statically without continuous energy input because the fluid locks the actuator in place. This is critical for applications like lifting platforms or brakes.
Pneumatic Limitation: Pneumatic systems require constant air pressure to maintain position, which wastes energy and risks load slippage if pressure drops.
4. Durability in Harsh Environments
Hydraulic Advantage: Hydraulic systems perform reliably in extreme conditions (high temperatures, heavy contamination, or shock loads). The oil lubricates components, reducing wear.
Pneumatic Limitation: Moisture in compressed air can cause corrosion in pneumatic systems, and contaminants (dust, humidity) degrade performance.
5. Compact Design for High Power
Hydraulic Advantage: Smaller hydraulic actuators can deliver the same force as larger pneumatic ones due to higher operating pressures. This saves space in machinery design.
Example: A hydraulic cylinder with a 2-inch diameter can generate over 30,000 lbs of force at 10,000 PSI, while a pneumatic cylinder of the same size produces only ~300 lbs at 150 PSI.
6. Continuous Operation Without Overheating
Hydraulic Advantage: Hydraulic oil acts as a coolant, allowing systems to run continuously without overheating.
Pneumatic Limitation: Compressing air generates heat, and prolonged use can cause pneumatic components to overheat, requiring downtime.
7. Versatility in Speed and Torque
Hydraulic Advantage: Hydraulic motors and actuators can achieve variable speeds and torque without gear reduction, making them ideal for applications like winches or conveyor systems.
Pneumatic Limitation: Pneumatic motors struggle to maintain consistent torque at low speeds.
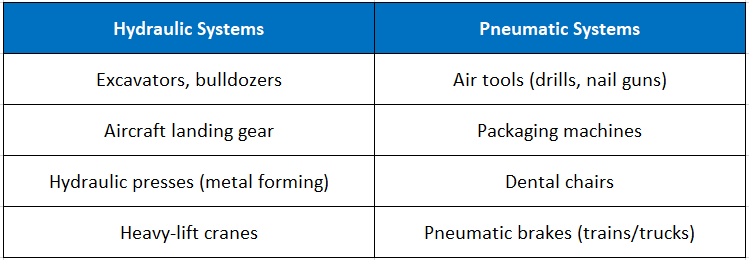
When to Choose Pneumatics Instead
While hydraulics excel in high-force and precision applications, pneumatics are preferable for:
Lightweight, clean environments (e.g., food processing, electronics).
Fast, repetitive motions (e.g., pick-and-place robots).
Explosive atmospheres (compressed air is non-flammable).
Hydraulic systems outperform pneumatic systems in high-force, precision, and heavy-duty applications due to their power density, controllability, and durability. However, the choice ultimately depends on the specific requirements of the application, including cost, environment, and force needs. For industries like construction, mining, and aerospace, hydraulic systems remain indispensable for their unmatched ability to handle extreme loads with precision.