Troubleshooting Hydraulic Cylinder Issues: Fixing Sticking, Slow Operation, or Failure to Actuate
Hydraulic cylinders are critical components in machinery across industries, from construction to manufacturing. When they malfunction—experiencing sticking, slow movement, or complete failure to actuate—it can disrupt operations and lead to costly downtime. In this SEO-optimized guide, we’ll explore common causes of hydraulic cylinder issues and actionable solutions to restore peak performance.
Common Symptoms of Hydraulic Cylinder Problems
Sticking or Jerky Movement
The cylinder hesitates, vibrates, or moves unevenly.
Slow Operation
The cylinder extends/retracts slower than normal.
No Movement
The cylinder fails to actuate despite hydraulic pressure.
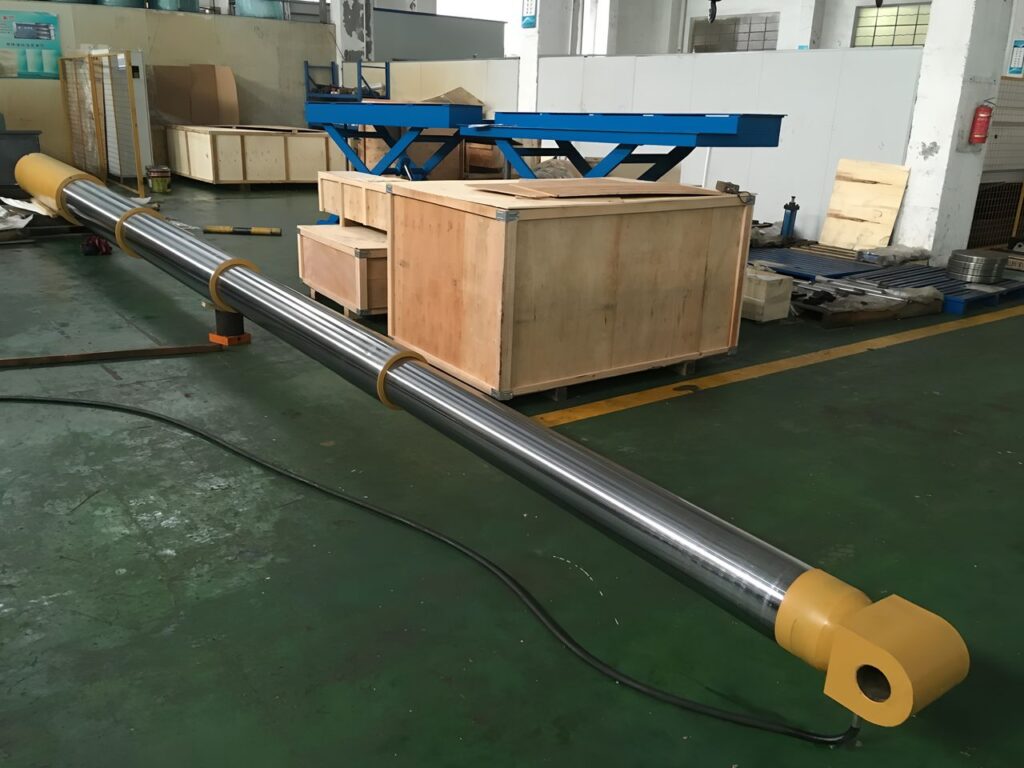
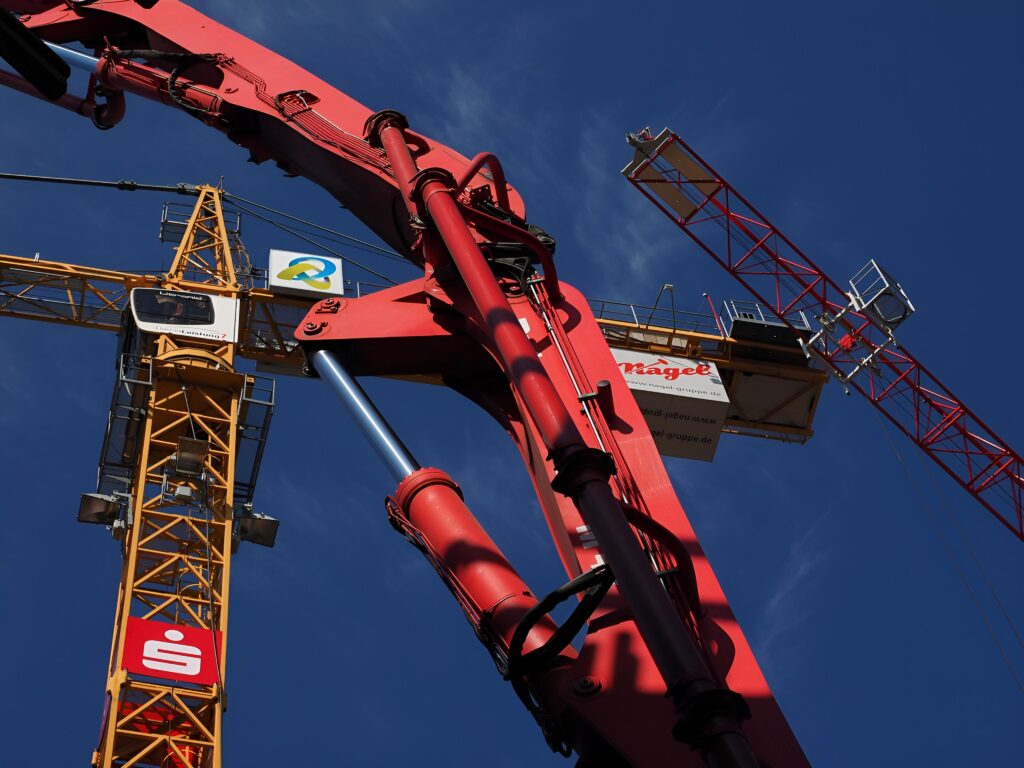
Top Causes of Hydraulic Cylinder Malfunctions
1. Contaminated Hydraulic Fluid
Issue: Dirt, debris, or water in the fluid can clog valves, damage seals, or score cylinder walls.
Signs: Erratic movement, increased wear.
Fix: Replace filters, flush the system, and use clean, high-quality hydraulic oil.
2. Air Entrapment (Aeration/Cavitation)
Issue: Air bubbles in the fluid reduce pressure efficiency, causing spongy or delayed motion.
Signs: Foamy fluid, unusual noises (whining/knocking).
Fix: Bleed air from the system, check for leaks, and ensure proper fluid levels.
3. Internal or External Leaks
Issue: Worn seals, damaged rods, or cracked hoses allow fluid to escape, reducing pressure.
Signs: Fluid puddles, slow speed, or loss of force.
Fix: Inspect/replace seals, repair damaged components, and pressure-test the system.
4. Worn or Damaged Components
Issue: Bent rods, scored barrels, or worn piston seals create friction and inefficiency.
Signs: Metal shavings in fluid, visible cylinder damage.
Fix: Rebuild or replace the cylinder, and inspect adjacent components (pumps, valves).
5. Incorrect Fluid Viscosity or Level
Issue: Too-thick fluid slows flow; low fluid levels starve the system.
Signs: Overheating, sluggish response.
Fix: Use manufacturer-recommended oil and maintain proper fluid levels.
6. Faulty Control Valves or Pump Issues
Issue: Malfunctioning valves or weak pumps fail to deliver adequate pressure/flow.
Signs: Inconsistent operation across multiple cylinders.
Fix: Test/replace valves, inspect pump performance, and check pressure settings.
Step-by-Step Solutions to Restore Cylinder Performance
Diagnose the Problem
Check for leaks, test fluid quality, and inspect visible components.
Clean or Replace Hydraulic Fluid
Flush the system and install new filters to eliminate contaminants.
Bleed Air from the System
Follow manufacturer guidelines to purge air pockets.
Repair or Replace Damaged Parts
Swap out worn seals, rods, or hoses; consider professional rebuilding for severe damage.
Verify System Pressure and Flow
Use gauges to ensure pumps and valves meet specifications.
Preventive Maintenance Tips
Regular Inspections: Check seals, fluid levels, and hoses monthly.
Filter Changes: Replace filters per the equipment manual.
Temperature Control: Avoid overheating, which degrades fluid and seals.
Use Quality Fluids: Invest in OEM-recommended hydraulic oils.
Hydraulic cylinder issues like sticking, slow operation, or failure to move can stem from fluid contamination, leaks, worn parts, or pressure irregularities. Regular maintenance and prompt troubleshooting are key to minimizing downtime. For persistent problems, partner with a trusted hydraulic service provider to ensure long-term reliability.