Choosing Seal Types and Tolerance Fits for Hydraulic Cylinders in Construction Machinery
Technical Guide for Enhanced Performance
Introduction:
Hydraulic cylinders are the backbone of construction machinery, powering critical operations in excavators, cranes, bulldozers, and more. However, their reliability hinges on two often-overlooked factors: seal selection and tolerance design. Poor choices in these areas lead to leaks, premature wear, and costly downtime. This article explores how to optimize seal configurations and tolerance fits for hydraulic cylinders, ensuring durability in harsh construction environments while boosting SEO visibility for manufacturers and suppliers.
1. Why Seal Types and Tolerances Matter in Construction Machinery
Hydraulic cylinders in construction equipment face extreme conditions:
High Pressure: Up to 40 MPa in heavy-duty applications like excavator arms.
Dynamic Loads: Frequent starts/stops and side forces during digging or lifting.
Environmental Hazards: Dust, moisture, temperature swings (-40°C to 120°C), and chemical exposure.
A mismatched seal or improper tolerance can cause:
➜ Fluid Leaks (loss of efficiency, environmental fines)
➜ Seal Extrusion (under high pressure)
➜ Friction-Induced Heat (accelerated wear)
➜ Cold Weather Failures (seal hardening)
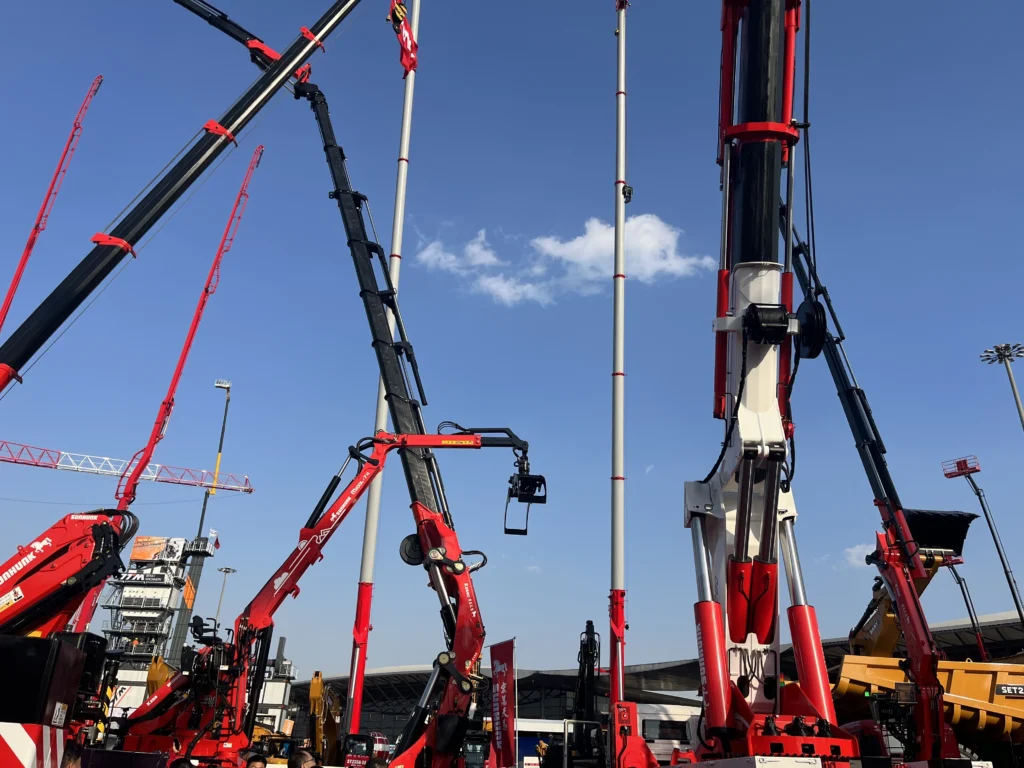
2. Key Seal Types for Construction Machinery Hydraulic Cylinders
A. Piston Seals (Primary Sealing)
O-Rings with Backup Rings
Best For: Low-to-medium pressure (≤25 MPa), static/low-speed applications.
Material: NBR (nitrile) for cost-effectiveness; FKM (fluoroelastomer) for high temperatures.
Critical Tip: Add PTFE backup rings at >15 MPa to prevent extrusion.
Composite Seals (e.g., Glyd Rings, Step Seals)
Best For: High-pressure (40 MPa), high-speed systems (e.g., excavator boom cylinders).
Design: Combines elastomer (sealing) + thermoplastic (wear resistance).
SEO Keyword: “high-pressure hydraulic cylinder seals.”
U-Cup Seals
Best For: Slow-moving, heavy-load applications (e.g., bulldozer tilt cylinders).
Advantage: Self-energizing design resists contamination.
B. Rod Seals (Dynamic Sealing)
Double-Lip Y-Seals
Best For: High-speed piston rods (1 m/s+) in cranes or loaders.
Material Upgrade: TPU (thermoplastic polyurethane) improves wear resistance by 200%.
Scraper-Seal Combinations
Best For: Multi-stage contamination control in mining or tunnel equipment.
C. Wear Rings and Guide Bands
Function: Reduce metal-to-metal contact, absorb side loads.
Materials: PTFE, phenolic resin, or carbon-filled composites.
SEO Keyword: “hydraulic cylinder wear ring solutions.”
3. Tolerance Design: Balancing Precision and Performance
A. Tolerance Guidelines by Component

B. Surface Finish Requirements
Piston Rod: Hard chrome plating (0.03–0.05 mm) + polishing (Ra ≤0.2 μm).
Cylinder Bore: Honed or roller-burnished (Ra 0.1–0.4 μm).
C. Temperature Compensation
Cold Climates: Increase clearances (e.g., H9/f8) to accommodate seal contraction.
High Heat: Use FKM seals and tighter fits (H7/g6) to counter thermal expansion.
Selecting the right hydraulic cylinder seals and tolerance fits is pivotal for construction machinery performance. By aligning seal materials (NBR, FKM, TPU) with operational demands and adhering to precision tolerance standards (H8/f7, H9/g6), manufacturers can dramatically reduce downtime and maintenance costs.
For engineers and procurement managers seeking durable hydraulic cylinder solutions, understanding these technical nuances ensures machinery that withstands the toughest job sites. Bookmark this guide for quick reference, and explore our product catalog for industry-leading seals and components engineered for construction excellence.